And the Top 4 MIG welding tips are...
#1 MIG welding tip...Get a better Ground clamp.
This is probably one of the most important mig welding tips ever!
Ever heard someone light up with a mig gun and it sounds like a drive-by shooting?
You know what’s wrong? Bad ground!
That’s right a bad ground.
It is such a simple fix but I hear that sound all the time.
People have trashed machines and bought new ones for this reason alone and all the while, all that was wrong was a bad ground. Why? Have you paid close attention to ground clamps recently? They suck! I mean they really suck! It used to be that ground clamps were made from copper. Now they are plated steel with a tiny piece of copper on the jaws.
Guess what? The old ones are better.
You could say that about a lot of things right? But here’s a secret: you can still buy the old ones. It is no secret that copper is the best conductor. That’s why copper ground clamps are better. Especially ones that have a strong ass spring.
Bottom line is...in order to get good starts, you need a really good ground. I have a secret weapon that I use to get a good ground. And it involves copper..

Mig Welding Tip ...A Better Ground...
#2 Mig welding tip... Watch Your Stickout.
The second most important of Mig welding tips is "stickout"
Stickout is misunderstood. What it really means is the distance from the mig welding tip (also called contact tip) to the arc.
Not the distance from the nozzle to the arc!
Too long a stickout will soften the arc and make the weld pile up.
A longer stickout works ok and can be a good thing on really thin sheet metal like body panels.
and for high amperage spray transfer a longer stickout is preffered.
But if you want a good crisp arc using short circuit mig on thicker metal, keep the stickout less than 1/2 inch.
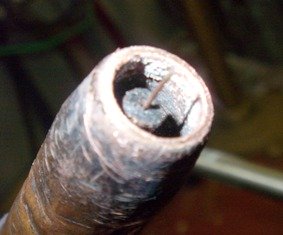
tip recessed= too much stickout=gorilla welds
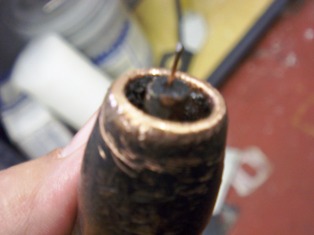
Thats better...tip poking out= shorter stickout = better penetration and smoother welding on thicker metals.
some welding companies offer different nozzle /contact tip combinations for different types of mig welding but other times, you might need to trim the nozzle.
#3 MIG Welding Tip..Learn to weld Uphill
Another of many important MIG welding tips is to Weld Uphill on anything thicker than 1/4". Just look at the lack of fusion in the photo below.
this was a good looking weld but it hardly has any penetration at all.
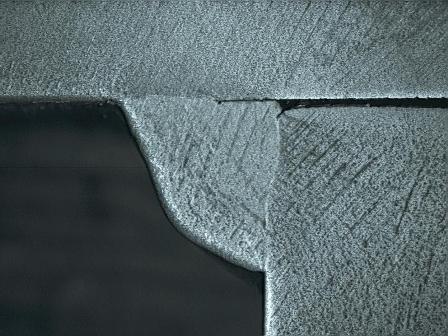
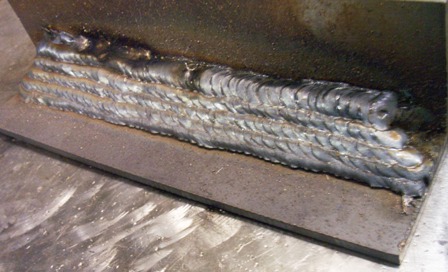
That opening on the bottom bead was a real eye opener for the student who welded it.
The weld above is a lap joint welded first and a tee joint done on top of the lap to conserve metal.
After stacking lots of beads on the tee, the stress pulled the lap joint weld loose.
That bead just didnt penetrate.
#4 Mig Welding Tip...get a good Auto darkening Helmet
I Know there were only supposed 3 Mig welding tips...But this one is probably as important as any...
Even moving a quarter inch off track when you nod your helmet down can really screw things up with mig welding. Why? Because Your mig welder does not care about you.
Mig machines just start laying down metal without concern for your well being or whether or not you are on track. With an Auto Darkening helmet you can see where your wire is pointing before you pull the trigger.
Leave a comment